Flexible Printed Circuit Design: Tips for Success in Your Next Project
Flexible Printed Circuit (Flex PCB) has revolutionized the electronics industry by offering a compact, lightweight, and versatile solution for interconnecting electronic components. These thin, flexible, and bendable circuit boards are now a staple in various applications, from consumer electronics to aerospace technology.
Understanding the Basics of Flexible Printed Circuit
Flex PCBs, also known as flex circuits, are thin and lightweight alternatives to rigid PCBs. They consist of a thin layer of flexible dielectric material, typically polyimide or polyester, with copper traces etched onto it. These traces provide the electrical connectivity between various components on the circuit. The flexible nature of these circuits allows them to conform to irregular shapes, making them ideal for applications where space and weight constraints are crucial.
Flexible Printed Circuit: Market Insights and Analysis
The FPC market has been on a continuous upswing, with a compound annual growth rate (CAGR) that shows no signs of slowing down. This growth is primarily attributed to the surging demand for flexible, lightweight, and space-saving electronic components. The FPC industry’s market size and value are expected to soar, thanks to the following factors:
1. Consumer Electronics: As consumer electronics become more compact and multifunctional, FPCs are indispensable in providing the required flexibility and space-saving solutions. They are found in smartphones, tablets, laptops, and wearables, enhancing the overall user experience.
2. Automotive Electronics: The automotive industry is embracing FPCs for their durability, flexibility, and resistance to harsh environmental conditions. FPCs are used in various applications, from infotainment systems to advanced driver-assistance systems (ADAS).
3. Medical Devices: The medical sector is witnessing a proliferation of cutting-edge devices. FPCs play a crucial role in these devices due to their flexibility, biocompatibility, and reliability. Applications include medical sensors, imaging equipment, and monitoring devices.
4. Telecommunication: With the expansion of 5G networks and the increasing demand for high-speed data transfer, FPCs are essential for connecting various components in network infrastructure.
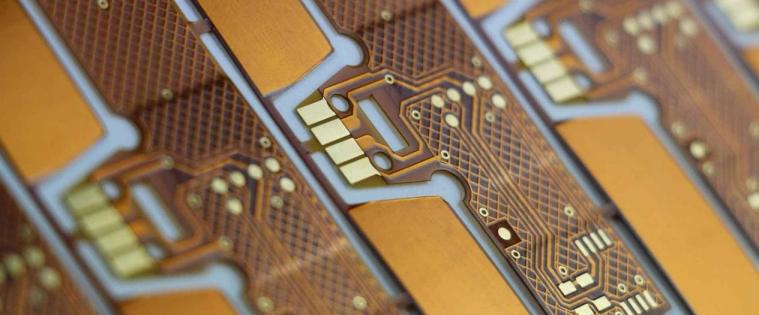
Tips for Success in Your Flexible Printed Circuit Project
1. Define Your Project Requirements Clearly: Before you dive into designing an FPC, it’s essential to establish clear project requirements. What are your size, shape, and performance expectations? The more precise your specifications, the better Winow New Energy can assist you in achieving your goals.
2. Choose the Right Materials: FPCs can be manufactured using various materials, each with distinct properties. Selecting the right material is crucial for ensuring the circuit’s durability, flexibility, and thermal resistance. Winow New Energy offers a wide range of material options to suit your needs.
3. Consider Design Constraints: When designing your flexible PCB, consider factors like bend radius, layer count, and the location of components. Winow New Energy’s team can help you optimize your design to meet these constraints effectively.
4. Quality Assurance and Testing: Rigorous testing is vital for ensuring the reliability of FPCs. Collaborate with a manufacturer like Winow New Energy that has robust quality control processes in place to meet the highest industry standards.
5. Consult with Experts: When in doubt, don’t hesitate to seek expert guidance. Winow New Energy’s team of professionals can provide valuable insights and assist you in overcoming any design challenges you may encounter.
Flexible Printed Circuit: Troubleshooting Flex PCB Issues
Flexible Printed Circuit is not immune to challenges, and troubleshooting can be a complex task. However, understanding common issues and their solutions can help you overcome these challenges effectively.
Troubleshooting Flex PCB Issues: Common Challenges and Solutions
Issue 1: Delamination
Delamination is the separation of layers in a Flex PCB, and it can occur due to various factors, such as poor material choice or inadequate adhesion during manufacturing.
Solution: To prevent delamination, choose high-quality materials and ensure proper lamination during manufacturing.
Issue 2: Cracking
The thin and flexible nature of Flex PCBs makes them susceptible to cracking, especially at fold lines or stress points.
Solution: Use reinforced or thicker areas at critical bending points and incorporate appropriate bending radii.
Issue 3: Connector Failures
Connectors can experience excessive wear and tear in Flex PCBs due to repeated flexing.
Solution: Choose robust connectors and consider options like ZIF (Zero Insertion Force) connectors to reduce wear and tear.
Flexible Printed Circuit: Supply Chain and Sourcing
The supply chain for flexible printed circuits is intricate, involving various stages from materials sourcing to manufacturing processes. Understanding this supply chain is crucial for both buyers and manufacturers looking to ensure the reliability and quality of FPCs. Here’s a breakdown of the key components:
Flexible Printed Circuit: Materials
1. Substrates: The base material for FPCs can be made of polyimide, polyester, or other flexible materials, depending on the specific requirements of the application.
2. Copper Foils: Copper foils are used for the conductor traces on FPCs. The thickness and quality of copper foils significantly impact the FPC’s performance.
3. Adhesive and Coverlay Films: These materials are used to bond layers and provide insulation, protection, and rigidity to the FPC.
Flexible Printed Circuit: Manufacturing Processes
1. Etching: This is a critical process in FPC manufacturing where unwanted copper is removed using a chemical etchant to create the desired circuit pattern.
2. Solder Mask Application: Solder mask application is essential to protect copper traces from oxidation and ensure solderability.
3. Component Mounting: Components such as chips, connectors, and integrated circuits are assembled on the FPC, often using pick-and-place machines.
4. Testing and Inspection: Quality control is vital in FPC manufacturing, including electrical testing and visual inspection to ensure the function of the circuit as intended.
5. Final Assembly: After all components are mounted and the FPC is verified for quality, it is integrated into the final product.
Meet the Flexible Printed Circuit Manufacturer
For your Flex PCB project, you need a reliable and experienced manufacturer to ensure success. Winow New Energy Co., LTD, based in Dongguan, is a leading manufacturer of flexible printed circuits.
They offer a wide range of design and manufacturing services to meet your specific project requirements. With their expertise and state-of-the-art facilities, you can trust them to deliver high-quality Flex PCBs for your applications.
Conclusion
In conclusion, understanding the world of Flexible Printed Circuit and following the right design practices are essential for a successful project. By selecting the appropriate materials, designing with flexibility in mind, and addressing common issues, you can harness the full potential of Flex PCBs in your next electronic venture. With a reputable manufacturer like Winow New Energy Co., LTD, you can ensure your Flex PCB project is in capable hands. Happy designing!