Circuit Board Assembly: Tips and Techniques for Success
When creating electronic equipment, circuit board assembly is a critical part of the production process. Everything from basic gadgets to sophisticated machinery must be built with precision and accuracy in mind. To assist in this effort, Winow New Energy Company – an experienced provider of circuit board assembly services – has shared insight into the key elements and necessary protocols for producing high-quality boards. Here, we’ll take a look at the most beneficial tips and strategies available to satisfy your circuit board assembly needs.
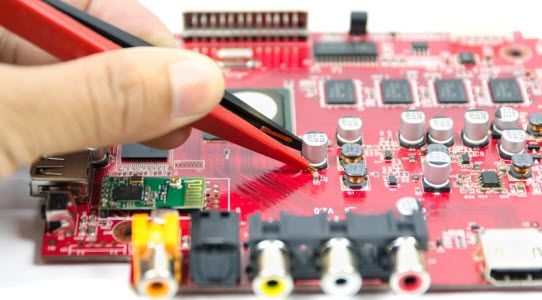
I. Understanding the Requirements of Circuit Board Assembly
1. Components and Specifications:
Before embarking on the assembly process, it is vital to understand the components and specifications of the circuit board thoroughly. Different electronic devices require specific components, such as resistors, capacitors, integrated circuits, and connectors, among others. Familiarizing oneself with the necessary components and their corresponding specifications will ensure accurate assembly and compatibility.
2. Quality Control and Testing:
Maintaining strict quality control measures is paramount in circuit board assembly. Each component must be carefully inspected for defects or damage before assembly. Additionally, rigorous testing procedures should be implemented throughout the assembly process to identify any potential issues. This proactive approach will help prevent costly reworks and ensure a higher level of customer satisfaction.
II. Tips for Circuit Board Assembly
1. Component Selection and Preparation:
Choosing the right components and preparing them adequately is vital for a smooth assembly process. Here are a few key considerations:
Component Quality and Compatibility: Ensure the components selected meet the required quality standards and are compatible with the circuit board design. Using reputable suppliers and performing thorough component testing can help prevent failures and performance issues.
Proper Component Storage: Store components in appropriate conditions, such as controlled temperature and humidity environments, to prevent damage due to moisture or static electricity. Implementing proper storage practices ensures the components remain in optimal condition until assembly.
2. PCB Design and Layout Optimization:
The design and layout of the printed circuit board (PCB) significantly impact the ease of assembly and overall functionality. Consider the following tips:
Component Placement: Optimize component placement on the PCB to minimize signal interference and ensure efficient assembly. Grouping related components together and considering the routing of critical signals can simplify the assembly process and enhance performance.
Clear Labeling and Marking: Clearly label components, traces, and reference designators on the PCB to avoid confusion during assembly. This reduces the chances of errors and helps technicians navigate the board accurately.
3. Manufacturing Process and Equipment:
Efficiency and precision in the manufacturing process can lead to improved assembly outcomes. Take note of the following aspects:
Automated Assembly: Leverage automated assembly equipment, such as pick-and-place machines and soldering robots, to enhance efficiency, accuracy, and consistency. Automated processes minimize human error and increase productivity, especially for complex circuit board assemblies.
Soldering Techniques: Adopt appropriate soldering techniques, such as reflow soldering or wave soldering, based on the specific requirements of the circuit board. Ensuring proper temperature profiles, solder paste application, and solder joint inspection can help achieve reliable and durable connections.
4. Quality Control and Testing:
Thorough quality control measures are essential to identify any defects or issues in the assembled circuit boards. Consider the following guidelines:
Inspection and Testing Procedures: Implement stringent inspection and testing procedures at various stages of assembly, including visual inspection, automated optical inspection (AOI), and functional testing. This ensures the detection of any faults or abnormalities early in the process.
Defect Analysis and Corrective Actions: Establish a robust system for defect analysis, documentation, and corrective actions. Analyzing defects can help identify potential weaknesses in the assembly process and drive continuous improvement efforts.
III. Best Practices for Circuit Board Assembly
1. Proper Handling and Storage:
Components used in circuit board assembly are often sensitive to environmental factors such as moisture, static electricity, and temperature fluctuations. Therefore, it is crucial to handle and store these components appropriately. Utilize anti-static measures, such as grounding straps and conductive storage containers, to prevent damage caused by electrostatic discharge. Additionally, store components in climate-controlled areas to preserve their integrity.
2. Accurate Placement and Soldering:
The precise placement of components on the circuit board is a critical step in the assembly process. Utilize automated assembly machines or meticulous manual techniques to ensure accurate positioning. When soldering, employ the appropriate techniques, such as surface mount technology (SMT) or through-hole soldering, depending on the board’s requirements. Maintain optimal soldering temperatures and use high-quality solder to achieve reliable connections.
3. Efficient Workflow and Documentation:
To enhance productivity and minimize errors, establish an efficient workflow for circuit board assembly. Plan the assembly process in a logical sequence, ensuring that each step is clearly defined and understood by the assembly team. Detailed documentation, including assembly instructions, diagrams, and bill of materials (BOM), is essential to provide clear guidelines and maintain consistency throughout the process.
Ⅳ. Leveraging Winow New Energy Company’s Expertise
Winow New Energy Company, a renowned manufacturer in the industry, has perfected the art of circuit board assembly. Their success can be attributed to their commitment to excellence and adherence to industry best practices. By leveraging their expertise, manufacturers can learn valuable lessons to achieve successful circuit board assemblies.
1. Continuous Training and Development:
Winow New Energy Company emphasizes the importance of continuous training and development for their assembly teams. By staying updated with the latest technologies, techniques, and industry standards, assembly technicians can enhance their skills and improve the overall quality of the assembly process.
2. Collaborative Approach:
Winow New Energy Company fosters a collaborative environment where cross-functional teams work together seamlessly. Encouraging open communication between design engineers, manufacturing engineers, and assembly technicians helps identify and address potential design or assembly issues at an early stage, ensuring smoother production cycles.
Conclusion:
Circuit board assembly requires a combination of technical expertise, attention to detail, and adherence to industry best practices. By understanding the requirements of circuit board assembly and implementing the tips and techniques discussed above, manufacturers can increase the likelihood of successful assembly outcomes. Drawing inspiration from industry leaders like Winow New Energy Company can provide valuable insights and guide manufacturers toward achieving high-quality circuit board assemblies. With precision and dedication, manufacturers can contribute to the production of reliable and efficient electronic devices.