HDI Customized Prototype Gerber Medical: A Closer Look
In today’s rapidly evolving medical industry, technology is constantly pushing boundaries, and one area that is seeing significant growth is customized prototype Gerber medical products.
With the emergence of 3D printing, the development of new materials, and the integration of advanced technologies such as AI and machine learning, medical device manufacturers can now create highly personalized products that meet the specific needs of patients.
One critical tool in this process is the use of HDI (high-density interconnect) technology. This approach enables the design of highly complex medical devices, which can be fabricated with exceptional accuracy and precision.
1. Customization is Key
Medical devices must be designed with precision and accuracy to ensure they function correctly and provide the intended results. Customization is therefore critical to meeting the unique needs of patients. A Gerber file is a standard format for printed circuit board (PCB) design data, and it is used in the design and manufacture of medical devices. The use of customized prototype Gerber medical products enables the design and fabrication of devices that are tailored to the specific requirements of individual patients.
These customizations can be as simple as adapting the shape or size of a medical device to better fit a patient’s anatomy. They can also be more complex, such as incorporating patient-specific data to ensure optimal performance. This level of customization allows medical professionals to provide treatments that are more effective and have a higher success rate.
2. Precision and Accuracy
HDI technology plays a crucial role in the development of customized prototype Gerber medical products. HDI technology involves the use of advanced manufacturing techniques to create high-density interconnects. This means that the individual components of a medical device can be placed closer together, allowing for smaller and more complex designs. HDI technology enables the creation of medical devices that are highly precise and accurate, with tolerances as small as 0.001 inches.
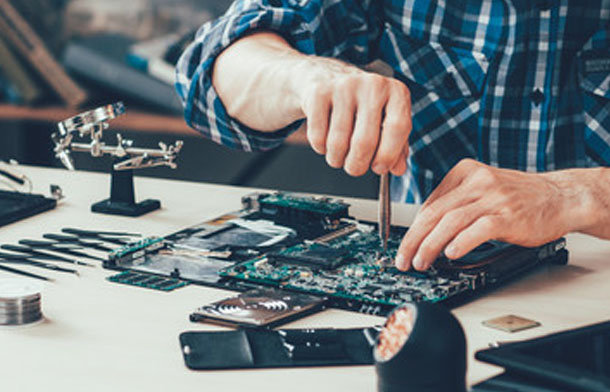
The use of HDI technology also results in a reduction in the size and weight of medical devices. This makes them easier to use and transport, particularly for surgical applications, where precision and mobility are critical factors.
3. Integration of Advanced Technologies
The development of customized prototype Gerber medical products also involves the integration of advanced technologies such as AI and machine learning. AI and machine learning can be used to analyze patient data, such as imaging and clinical data, to develop personalized medical devices that are specifically tailored to the patient’s unique requirements. These technologies also enable the development of predictive models that can help medical professionals anticipate potential issues and address them before they become problematic.
Advancing Medical Technology: HDI Customized Prototype Gerber Medical
Advancements in medical technology have made it possible to design and manufacture custom-printed circuit boards (PCBs) for medical devices that meet the highest quality standards. These PCBs are designed to meet specific requirements such as high reliability, accuracy, and safety, and are subject to strict regulations and standards. The manufacturing processes used to produce medical PCBs must adhere to strict guidelines to ensure that the final product is safe for use in medical settings.
Winow New Energy Co., Ltd. is a company that has been manufacturing custom-printed circuit boards for medical devices for more than 15 years. They provide complete PCB fabrication and engineering support for medical device engineers and designers, including prototyping, engineering support, and fabrication services. Their team provides engineering support services, consulting with customers to ensure they get the best possible PCBs.
Winow has long-standing, strategic partnerships with domestic and overseas PCB facilities capable of providing high-quality products at an affordable rate. Once they have finished manufacturing a PCB, they can help their customers with any problems or issues that may arise and help with the lifecycle of the product.
One-Stop Solution: Winow New Energy’s Customized Prototype Gerber Medical
Winow’s Customized Prototype Gerber Medical provides a one-stop solution for medical device manufacturers. Winow helps medical device engineers and designers by providing complete PCB fabrication and engineering support for their products. They can generate high-frequency, high-density interconnects that can be applied to medical devices.
What are PCBs, and why are they important in medical devices?
Printed Circuit Boards (PCBs) are boards made of insulating material such as fiberglass or plastic, with conductive pathways etched onto their surface. They are used in a wide range of electronic devices, from computers to medical equipment. In the context of medical devices, PCBs are used to build various electronic components such as sensors, controllers, and power supplies.
Medical PCBs are designed to meet the specific requirements of medical devices, such as high reliability, accuracy, and safety. Medical devices often require high precision and accuracy to produce accurate and reliable results. Therefore, the PCBs used in medical devices are designed and manufactured to strict standards to ensure their quality, reliability, and effectiveness.
Get Ready for Large-Scale Orders with Winow New Energy’s Customized Prototype Gerber Medical!
Medical PCBs are used in a wide range of electronic devices, from computers to medical equipment. However, in the context of medical devices, PCBs must meet strict quality and reliability standards to ensure that they are safe, accurate, and reliable for use in medical settings. Medical PCBs are used in patient monitoring devices, diagnostic imaging equipment, therapeutic devices, and laboratory equipment.
Designing medical-grade PCBs requires careful consideration of several important factors, including reliability, performance, safety, sterilization, traceability, documentation, and cost. PCBs must be designed with robust materials and manufacturing processes that can withstand harsh environments and repeated use. They must also be designed to minimize noise, interference, and other sources of signal degradation to ensure accurate and reliable performance.
Winow offers complete PCB fabrication and engineering support for medical device manufacturers. They provide PCB prototypes to test the design and PCB prior to going into production. Winow also provides engineering support services, consulting with their customers to ensure they get the best possible PCBs. They can help create PCBs that meet both financial and quality needs. Additionally, Winow has long-standing, strategic partnerships with domestic and overseas PCB facilities capable of providing high-quality products at an affordable rate.
Conclusion
Winow New Energy’s customized prototype Gerber Medical is an excellent solution for medical device manufacturers who need to ensure that their PCBs meet the specific requirements of the medical industry. With Winow’s expertise in PCB fabrication and engineering support, medical device manufacturers can be confident that their PCBs are safe, reliable, and effective for use in medical settings.