Low Volume PCB Assembly: A Comprehensive Guide
Low volume PCB assembly is a process that involves the production of small quantities of printed circuit boards (PCBs). This type of assembly is ideal for companies that need a limited number of PCBs for prototyping or small-scale production runs. Low volume PCB assembly is a cost-effective solution for businesses that require a small number of PCBs, as it eliminates the need for expensive tooling and setup costs associated with high volume production.
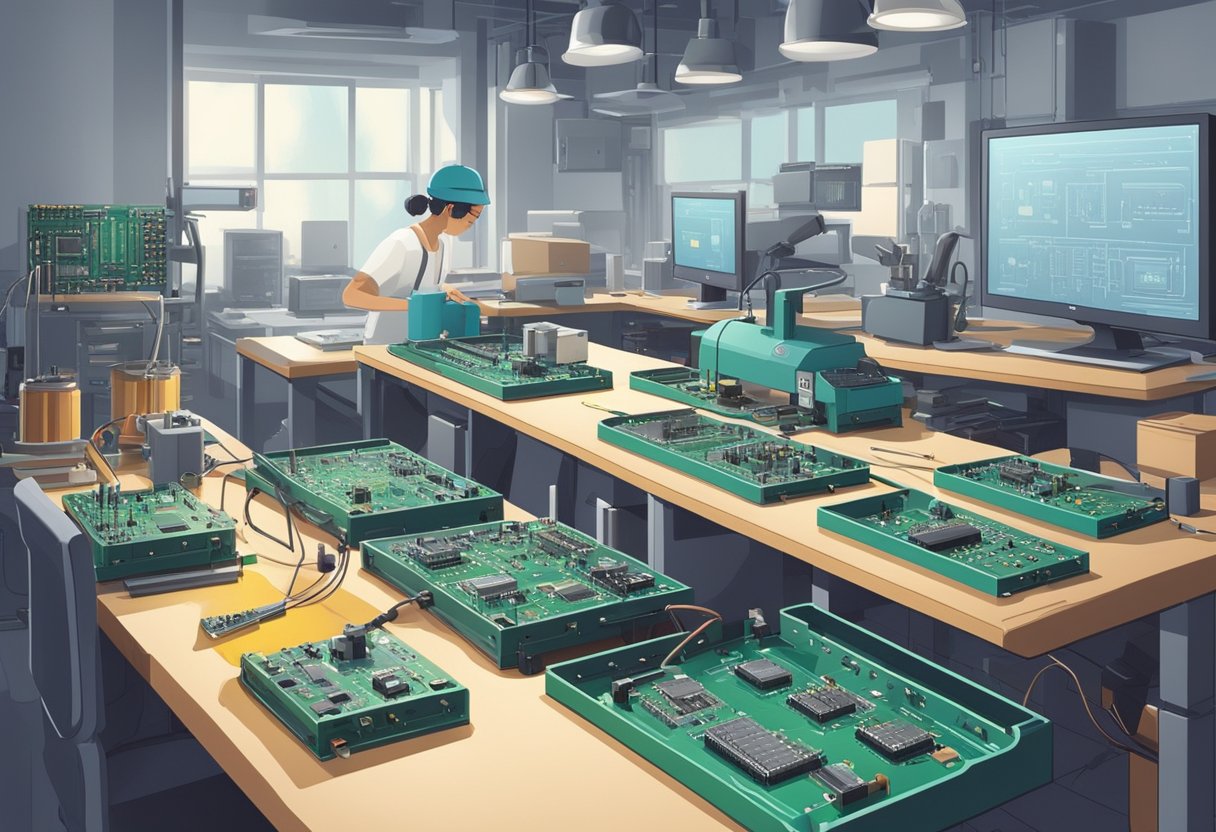
The process of low volume PCB assembly involves a number of steps, including design, component sourcing, PCB fabrication, assembly, and testing. Each of these steps is critical in ensuring the final product meets the required specifications. Design is the first step in the process and involves creating a schematic of the circuit that will be printed on the PCB. Component sourcing involves selecting the appropriate components to be used in the circuit, while PCB fabrication involves producing the physical board itself. Assembly involves placing the components on the board and soldering them in place, while testing ensures that the final product functions as intended.
Understanding Low Volume PCB Assembly
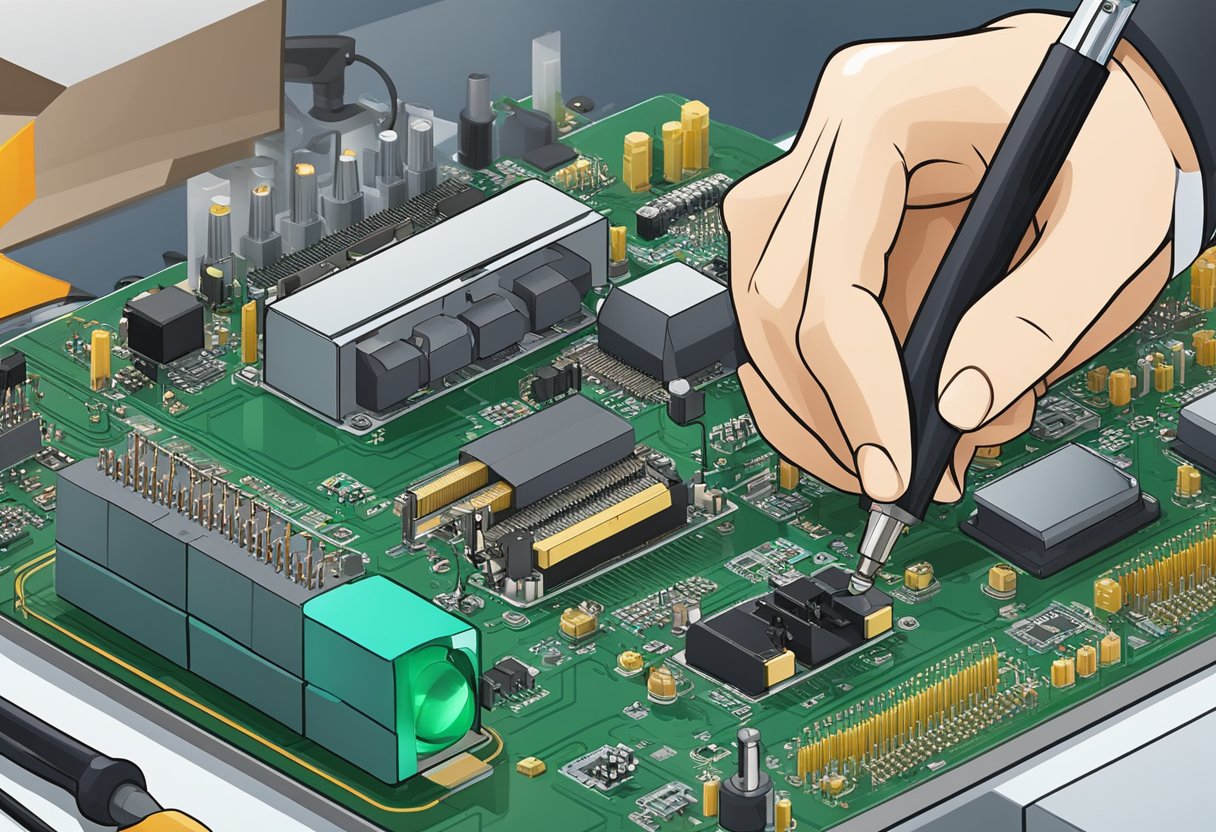
Low volume PCB assembly is the process of manufacturing a small number of printed circuit boards (PCBs) for prototypes, small-scale production, or specialized applications. It is a cost-effective and efficient way to produce PCBs in small quantities without incurring the high costs associated with high-volume production.
One of the advantages of low volume PCB assembly is that it allows for greater flexibility in the design and testing of electronic products. This is because it is easier and less expensive to make changes to the design of the PCB during the low volume production phase, compared to making changes during high-volume production.
Low volume PCB assembly typically involves manual assembly processes, such as surface mount technology (SMT) and through-hole technology (THT), as well as manual soldering and inspection. This is because automated assembly processes are not cost-effective for small quantities.
In addition, low volume PCB assembly requires close collaboration between the PCB manufacturer and the customer to ensure that the final product meets the customer’s specifications and requirements. This collaboration includes design review, prototype testing, and quality control to ensure that the final product is of high quality and meets the customer’s expectations.
Overall, low volume PCB assembly is an important process for the development and production of electronic products in small quantities. It offers flexibility, cost-effectiveness, and high-quality results that are essential for the success of small-scale production and specialized applications.
Benefits of Low Volume PCB Assembly
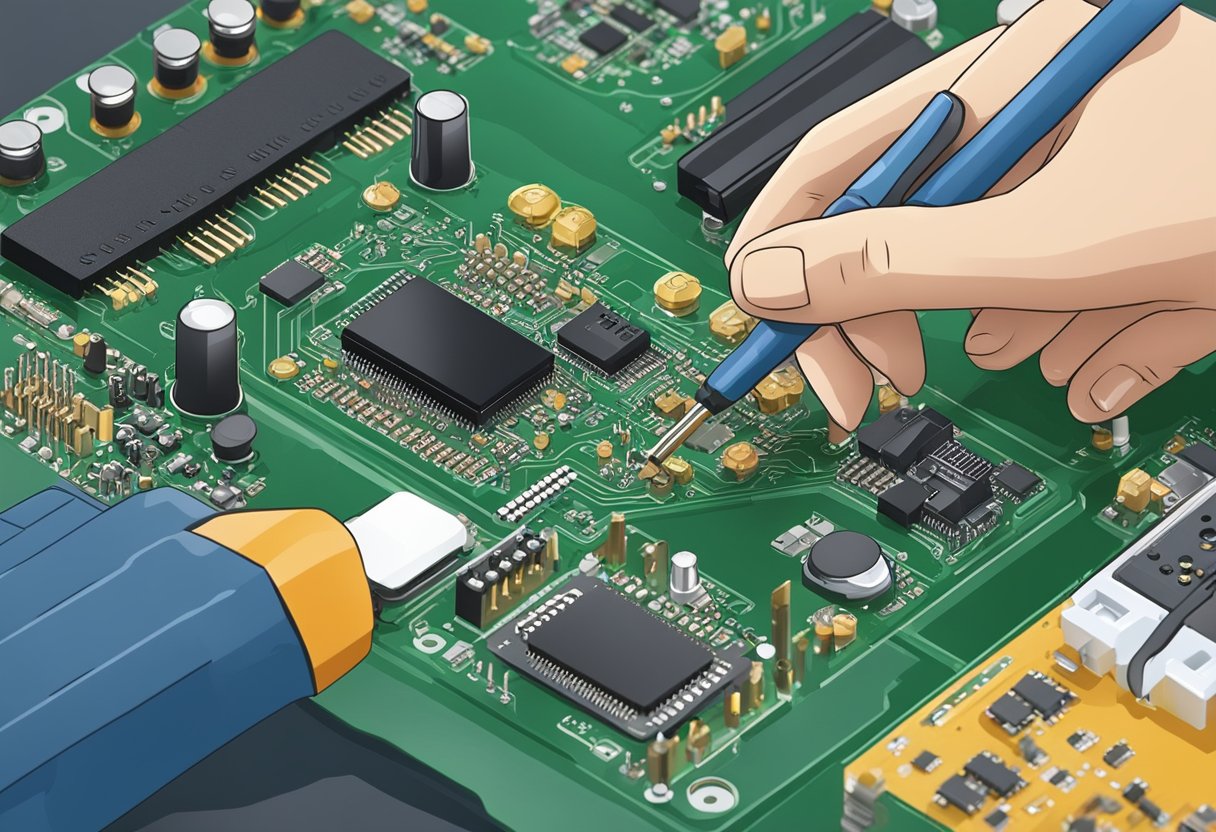
Low volume PCB assembly offers several benefits to companies that require small quantities of printed circuit boards. These benefits include cost efficiency, rapid prototyping, and customization and flexibility.
Cost Efficiency
One of the primary benefits of low volume PCB assembly is cost efficiency. With low volume assembly, companies can order small quantities of PCBs without incurring significant setup costs. This means that companies can save money on their PCB manufacturing costs, especially if they only need a small number of PCBs.
Rapid Prototyping
Another benefit of low volume PCB assembly is rapid prototyping. Companies can quickly produce a small number of PCBs to test their designs before committing to a larger production run. This allows companies to identify any design flaws or issues early on in the process, which can save time and money in the long run.
Customization and Flexibility
Low volume PCB assembly also offers customization and flexibility. Companies can order small quantities of PCBs with specific designs or features that meet their unique requirements. This allows companies to create custom PCBs that are tailored to their specific needs, rather than having to settle for off-the-shelf solutions.
Overall, low volume PCB assembly offers several benefits to companies that require small quantities of printed circuit boards. With cost efficiency, rapid prototyping, and customization and flexibility, companies can produce high-quality PCBs that meet their unique requirements without breaking the bank.
Design Considerations for Low Volume Production
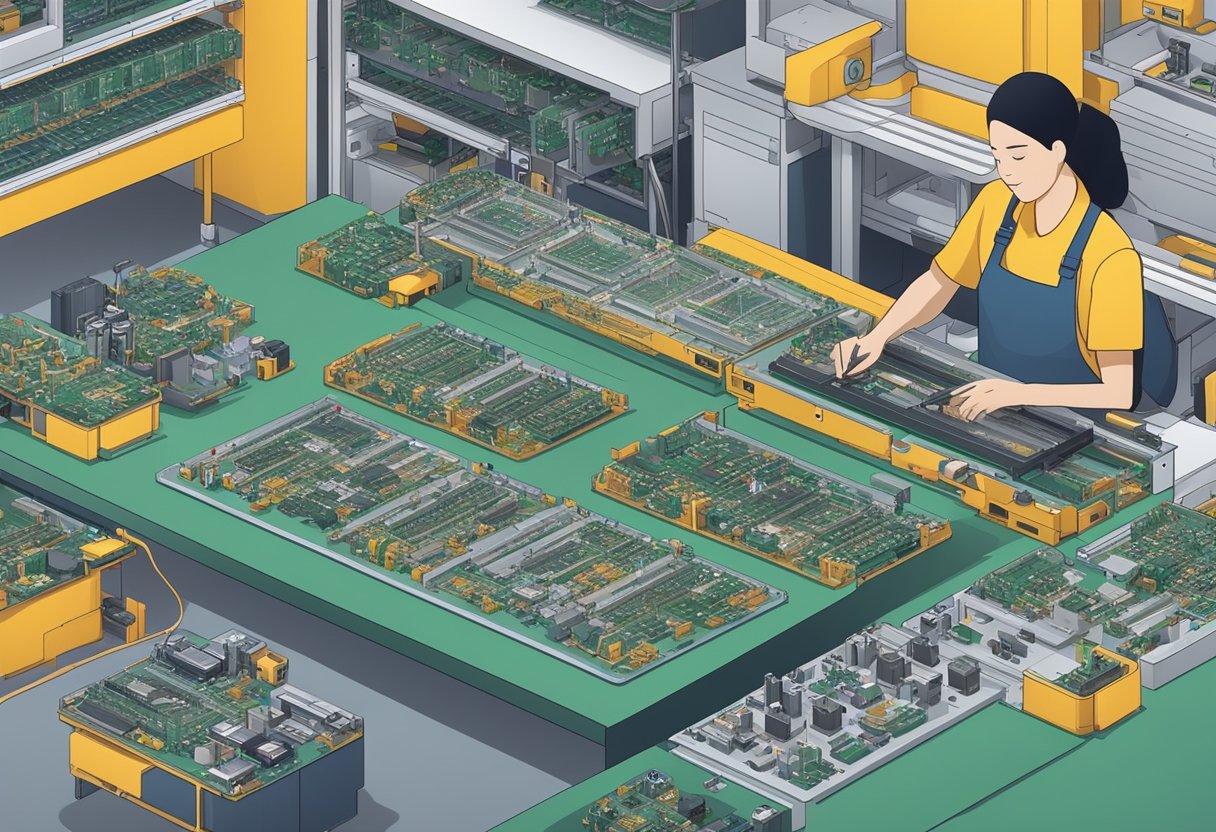
Component Sourcing
When it comes to low volume PCB assembly, sourcing components can be a challenge. Unlike high volume production where components are readily available, low volume production requires a different approach. In such cases, it is important to have a reliable supplier who can provide the necessary components in small quantities.
One option is to use off-the-shelf components that are readily available from distributors. However, this approach may not always be feasible, especially if the design requires custom components. In such cases, it is important to work with a supplier who can provide custom components in small quantities.
Design for Manufacturability
Design for manufacturability is an important consideration when it comes to low volume production. This involves designing the PCB in such a way that it can be easily and efficiently manufactured.
One key consideration is to minimize the number of components used in the design. This not only simplifies the assembly process but also reduces the cost of the PCB. Another important consideration is to use components that are easy to assemble and solder.
In addition, it is important to design the PCB with the manufacturing process in mind. This includes designing the PCB with the necessary tooling holes, fiducial marks, and other features that aid in the assembly process.
Overall, by considering component sourcing and designing for manufacturability, low volume PCB assembly can be made more efficient and cost-effective.
Choosing a PCB Assembly Partner
When it comes to low volume PCB assembly, choosing the right partner is crucial to ensuring the success of your project. Here are some factors to consider when selecting a PCB assembly partner:
Quality Certifications
One important factor to consider is whether your potential partner has the necessary quality certifications. Look for partners that have certifications such as ISO 9001, IPC-A-610, and/or AS9100. These certifications indicate that the partner has the necessary quality management systems in place to ensure consistent and reliable results.
Turnaround Time
Another important factor is the partner’s turnaround time. Look for partners that can provide you with a quick turnaround time without sacrificing quality. Make sure to ask about their lead times and whether they have any expedited options available.
Technical Capabilities
Finally, consider the partner’s technical capabilities. Look for partners that have experience with the types of PCB assemblies you need, as well as the specific components and materials you will be using. Ask about their testing capabilities and whether they have the necessary equipment to ensure your PCBs meet your specifications.
Overall, choosing the right PCB assembly partner is crucial to the success of your project. By considering factors such as quality certifications, turnaround time, and technical capabilities, you can find a partner that will meet your needs and help you achieve your goals.
PCB Assembly Processes
There are three main types of PCB assembly processes: Surface Mount Technology (SMT) assembly, Through-Hole assembly, and Mixed Technology assembly. Each process has its own advantages and disadvantages, and the choice of process depends on the specific requirements of the PCB.
SMT Assembly
SMT assembly is the most widely used PCB assembly process. It involves placing surface mount components directly onto the surface of the PCB. This process is faster and more efficient than Through-Hole assembly, as it eliminates the need for drilling holes in the PCB. SMT assembly also allows for smaller and lighter PCBs, as well as higher component density.
During SMT assembly, a solder paste is applied to the PCB, and the components are placed onto the paste. The PCB is then heated, causing the solder paste to melt and form a connection between the component and the PCB. SMT assembly requires specialized equipment, such as pick-and-place machines and reflow ovens.
Through-Hole Assembly
Through-Hole assembly involves placing components through holes drilled in the PCB and soldering them to the opposite side of the board. This process is slower and more labor-intensive than SMT assembly, but it is still used for certain components that cannot be surface-mounted or for applications that require high mechanical strength.
Through-Hole assembly requires the use of a wave soldering machine, which applies molten solder to the bottom of the PCB, causing it to flow through the holes and form a connection between the component and the PCB.
Mixed Technology Assembly
Mixed Technology assembly is a combination of SMT and Through-Hole assembly. This process is used when a PCB requires both surface-mounted and through-hole components. Mixed Technology assembly requires specialized equipment and a skilled operator to ensure that the components are placed correctly and that the solder joints are strong and reliable.
In conclusion, the choice of PCB assembly process depends on the specific requirements of the PCB. SMT assembly is faster and more efficient, while Through-Hole assembly is slower but provides higher mechanical strength. Mixed Technology assembly is used when a combination of both processes is required.
Testing and Quality Control
Low volume PCB assembly requires rigorous testing and quality control measures to ensure that the final product meets the customer’s specifications. In this section, we will explore the different types of testing and quality control measures used in low volume PCB assembly.
Automated Optical Inspection
Automated Optical Inspection (AOI) is a critical testing process used in low volume PCB assembly. AOI machines use high-resolution cameras to inspect the PCB for defects such as missing components, incorrect component placement, and solder joint defects. AOI machines are highly accurate and can detect defects that are difficult to detect with the naked eye.
Functional Testing
Functional testing is another important testing process used in low volume PCB assembly. This testing process involves testing the PCB to ensure that it performs its intended function. Functional testing is usually performed using specialized testing equipment that simulates the conditions in which the PCB will be used. This testing process ensures that the PCB meets the customer’s specifications and performs as expected.
In-Circuit Testing
In-Circuit Testing (ICT) is a testing process that involves testing individual components on the PCB. This testing process is used to detect defects in individual components such as resistors, capacitors, and diodes. ICT machines use specialized probes to test individual components and detect defects. This testing process ensures that the individual components on the PCB are functioning correctly and that the PCB meets the customer’s specifications.
In conclusion, testing and quality control are critical processes in low volume PCB assembly. These processes ensure that the final product meets the customer’s specifications and performs as expected. Automated Optical Inspection, Functional Testing, and In-Circuit Testing are the most commonly used testing processes in low volume PCB assembly.
Supply Chain Management
Low volume PCB assembly requires efficient supply chain management to ensure that the necessary components are available when needed. This involves working closely with suppliers and distributors to manage inventory levels and lead times.
One key aspect of supply chain management is ensuring that the right components are sourced from reliable suppliers. This requires careful evaluation of potential suppliers, taking into account factors such as quality, lead times, pricing, and availability. Once suppliers have been selected, it is important to establish clear communication channels to ensure that any issues or delays can be quickly addressed.
Another important aspect of supply chain management is inventory management. This involves tracking inventory levels and lead times to ensure that components are available when needed, without overstocking or understocking. Effective inventory management can help to reduce lead times and minimize the risk of production delays.
To streamline the supply chain, many low volume PCB assembly providers work with distributors who can provide a range of components from different suppliers. This can help to simplify the procurement process and reduce lead times, as distributors can often provide components more quickly than individual suppliers.
Overall, effective supply chain management is essential for successful low volume PCB assembly. By working closely with suppliers and distributors, and managing inventory levels carefully, providers can ensure that they have the components they need, when they need them, to deliver high-quality PCBs to their customers.
Cost Estimation and Budgeting
When it comes to low volume PCB assembly, cost estimation and budgeting are critical factors to consider. It is essential to have a clear understanding of the costs involved in the assembly process to avoid any unexpected expenses.
One of the primary factors that affect the cost of low volume PCB assembly is the quantity of PCBs required. Generally, the higher the quantity, the lower the cost per unit. However, for low volume production, the cost per unit is typically higher due to the setup and tooling costs involved.
Another factor that affects the cost of low volume PCB assembly is the complexity of the PCB design. Complex designs require more time and effort to manufacture, which can result in higher costs. It is essential to consider the complexity of the design when estimating the cost of low volume PCB assembly.
When budgeting for low volume PCB assembly, it is crucial to consider all the costs involved, including material costs, labor costs, setup and tooling costs, and shipping costs. It is also important to factor in any potential additional costs, such as design changes or unforeseen delays.
To ensure accurate cost estimation and budgeting, it is advisable to work with a reputable PCB assembly company that can provide detailed quotes and help you navigate the complexities of the assembly process. By working with an experienced partner, you can ensure that your low volume PCB assembly project is completed on time, within budget, and to the highest quality standards.
Challenges and Solutions in Low Volume Assembly
Lead Times
One of the biggest challenges in low volume PCB assembly is managing lead times. Since the production volumes are low, the lead times for components can be longer. This can result in delays in the production process, which can impact the delivery schedule.
To address this challenge, it is important to work closely with suppliers to ensure that components are ordered in a timely manner. It is also important to have a good understanding of the lead times for each component and to plan the production schedule accordingly. This can help to minimize delays and ensure that the project is completed on time.
Inventory Management
Another challenge in low volume PCB assembly is managing inventory. Since the production volumes are low, it can be difficult to justify the cost of holding a large inventory of components. However, not having the necessary components on hand can result in delays and impact the delivery schedule.
To address this challenge, it is important to have a good understanding of the components that are needed for each project. This can help to ensure that the necessary components are ordered in a timely manner and that inventory levels are kept at a minimum. It is also important to have a good system in place for tracking inventory levels and reordering components when necessary.
Overall, managing lead times and inventory levels are two of the biggest challenges in low volume PCB assembly. By working closely with suppliers and having a good understanding of the components that are needed for each project, these challenges can be addressed and the production process can be streamlined.
Future Trends in PCB Assembly
As technology continues to advance, there are several trends emerging in the PCB assembly industry. Here are a few of the most notable future trends:
Miniaturization
One of the most significant trends in PCB assembly is miniaturization. As electronic devices become smaller and more complex, the demand for smaller, more densely packed PCBs is increasing. This trend is driving the development of new assembly techniques, such as microelectronics and 3D printing.
Automation
Another trend in PCB assembly is the increasing use of automation. Automated assembly lines can improve efficiency, reduce costs, and increase production capacity. This trend is driving the development of new robotic assembly systems and software that can automate the entire assembly process.
Environmental Sustainability
Environmental sustainability is becoming an increasingly important consideration in PCB assembly. As consumers become more environmentally conscious, there is a growing demand for eco-friendly PCBs and assembly processes. This trend is driving the development of new materials and processes that are more sustainable and less harmful to the environment.
Smart Manufacturing
Finally, smart manufacturing is a trend that is transforming the entire manufacturing industry, including PCB assembly. Smart manufacturing uses advanced technologies such as the Internet of Things (IoT), artificial intelligence (AI), and big data analytics to optimize production processes, increase efficiency, and reduce costs. This trend is driving the development of new software and hardware solutions that can help manufacturers improve their operations and stay competitive in the global marketplace.
Overall, the future of PCB assembly looks bright, with new technologies and trends emerging that promise to revolutionize the industry. As these trends continue to develop, manufacturers will need to stay up-to-date with the latest advancements in order to remain competitive and meet the evolving needs of their customers.