PCB Assembly Quality Control Errors Ways to Prevent
PCB Assembly Quality Control is of supreme importance in today’s hi-tech world. WINOW, an illustrious business in the sector, places a strong emphasis on keeping up stringent standards. In this essay, we’ll discuss the key tactics used by WINOW to guarantee the quality of their PCB assembly services adheres to the industry’s peak requirements.PCB Assembly Quality Control.
1. Rigorous Component Inspection and Sourcing
WINOW understands that the foundation of high-quality PCB assembly lies in selecting reliable components. Before commencing the assembly process, they conduct thorough inspections of all components to ensure authenticity, functionality, and adherence to industry standards. Collaborating with trusted suppliers further enhances the sourcing process, minimizing the risk of counterfeit or subpar components.
2. Advanced Automated Optical Inspection (AOI)
To eliminate human error and detect subtle defects, WINOW relies on cutting-edge Automated Optical Inspection (AOI) systems. These state-of-the-art machines use high-resolution cameras and advanced algorithms to inspect every solder joint, and component placement, and trace for defects, ensuring a comprehensive examination of the PCB. AOI technology not only enhances accuracy but also expedites the inspection process, reducing production lead times.
3. Robust Design for Manufacturability (DFM) Guidelines
WINOW firmly believes that proactive quality control begins at the design stage. Their collaboration with design teams ensures adherence to Design for Manufacturability (DFM) guidelines. By considering manufacturing constraints during the design phase, they minimize potential pitfalls, such as assembly challenges and defects. This practice streamlines the entire production process and enhances the final product’s reliability.
4. Continuous Training and Skill Development
The commitment to quality control at WINOW extends to its workforce. They invest in continuous training and skill development programs for their assembly technicians and quality control inspectors. By staying updated on the latest industry practices and technological advancements, the team at WINOW is better equipped to identify and address potential quality issues, fostering a culture of excellence.
5. Comprehensive Testing and Prototyping
WINOW embraces a comprehensive approach to testing and prototyping, which aids in identifying and rectifying potential quality control errors early in the process. Rigorous functional testing, including in-circuit testing (ICT) and burn-in testing, helps ensure that the PCB Assembly Quality Control meet the specified performance parameters. Prototyping is also utilized to evaluate the assembly process and make necessary adjustments before full-scale production, reducing the likelihood of errors in the final product.
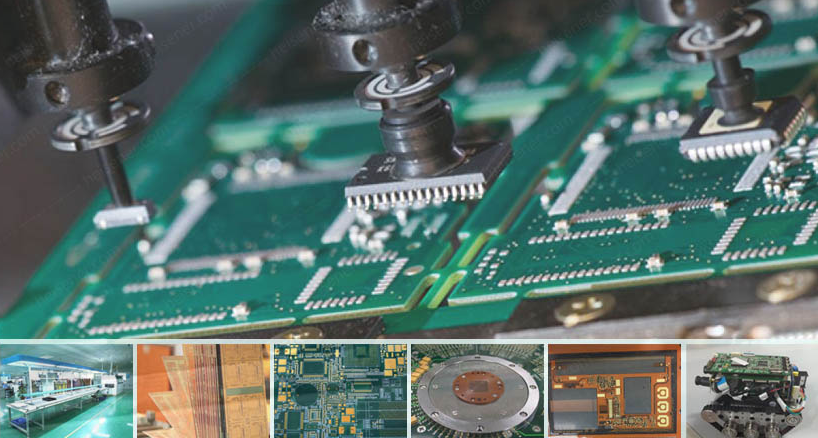
PCB Assembly Quality Control: 10 Quality Problems And Solutions Of PCB Products
1. Solder Joint Defects:
Solder joint defects can result in intermittent connections, reduced performance, and even failure of the PCB. To address this, WINOW employs automated optical inspection (AOI) machines to identify solder joint anomalies, ensuring proper alignment and solder distribution.
Solution: Implementing robust AOI inspections, along with manual checks by skilled technicians, guarantees high-quality solder joints in WINOW PCB products.
2. Component Misplacement:
Incorrectly placed components can lead to circuit malfunction or short circuits. To overcome this issue, WINOW utilizes advanced pick-and-place machines with precise positioning capabilities.
Solution: Regular calibration and maintenance of pick-and-place machines, combined with visual inspections, are vital to verifying accurate component placement.
3. Insufficient Solder Paste:
Inadequate solder paste application can result in weak joints and incomplete connections. WINOW tackles this challenge by using automated solder paste inspection (SPI) machines to ensure the correct amount of solder is applied.
Solution: SPI checks before assembly, along with real-time monitoring during the process, guarantee optimal solder paste application on WINOW PCBs.
4. Tombstoning:
Tombstoning occurs when a component partially lifts from one pad during reflow soldering. This issue can be mitigated through proper stencil design and appropriate reflow profiles.
Solution: WINOW optimizes stencil designs and reflow profiles, and the use of solder paste with appropriate viscosity to minimize tombstoning occurrences.
5. Solder Bridging:
Solder bridging occurs when solder connects adjacent components, causing shorts. WINOW employs selective soldering machines to reduce the risk of solder bridging, particularly in complex PCB designs.
Solution: By carefully programming selective soldering machines and conducting visual inspections, WINOW ensures minimal solder bridging in their products.
6. Warping and Delamination:
During the PCB assembly process, excessive heat or inadequate material bonding can lead to warping and delamination, affecting the overall product reliability.
Solution: WINOW adheres to strict temperature profiles during the assembly process and conducts reliability tests to identify and rectify warping and delamination issues.
7. Electrostatic Discharge (ESD) Damage:
ESD can damage sensitive electronic components, leading to premature failure. WINOW takes preventive measures by incorporating ESD-safe workstations and using proper packaging materials.
Solution: ESD training for employees and the implementation of ESD-safe handling practices help minimize the risk of ESD damage to WINOW PCB products.
8. Inadequate Conformal Coating:
Conformal coatings protect PCBs from moisture, dust, and other contaminants. WINOW employs automated coating machines to ensure even and thorough application.
Solution: Routine inspections and environmental testing validate the effectiveness of conformal coatings on WINOW PCBs.
9. Inconsistent Trace Widths:
Inconsistent trace widths can lead to impedance mismatches and signal integrity issues. WINOW employs high-precision manufacturing processes to maintain uniform trace widths.
Solution: Regular verification through high-resolution imaging and electrical testing ensures consistent trace widths in WINOW PCB products.
10. Poor Quality Materials:
Using substandard materials can significantly impact the performance and reliability of PCBs. WINOW maintains partnerships with reputable suppliers and conducts thorough material inspections before production.
Solution: WINOW’s commitment to sourcing high-quality materials and rigorous material testing guarantees the reliability of its PCB products.
Conclusion
In conclusion, achieving exceptional PCB Assembly Quality Control requires a multifaceted approach that encompasses various stages of production. As a leading manufacturer in the industry, WINOW understands the significance of implementing stringent quality control measures. By meticulously inspecting components, employing advanced AOI technology, adhering to DFM guidelines, investing in continuous training, and conducting comprehensive testing and prototyping, WINOW has successfully elevated the standard of their PCB assemblies. These strategies serve as valuable insights for other manufacturers seeking to enhance their own quality control processes and deliver reliable and high-performance electronic devices to the market.