PCB Board Manufacturing: Process Technology
PCB board manufacturing is a crucial process that forms the backbone of modern electronics. These intricate boards serve as the foundation for electronic devices, ranging from smartphones and laptops to complex industrial machinery. Understanding the PCB manufacturing process technology is essential for manufacturers like WINOW to produce high-quality, reliable, and efficient circuit boards. This blog will delve into the various stages of PCB board manufacturing, shedding light on the requirements and methodologies used by WINOW, a leading player in the industry.pcb board manufacturing.
Stage 1: Design and Prototyping
The initial step in PCB board manufacturing is the design and prototyping phase. Engineers at WINOW work closely with clients to create a comprehensive layout based on their specific requirements and device functionality. Advanced computer-aided design (CAD) software is employed to translate the schematic into a digital blueprint. This design then undergoes prototyping to validate its functionality and identify any potential flaws or improvements. Prototyping allows for adjustments to be made before moving to full-scale production, ensuring the best possible end result.
Stage 2: Material Selection and Preparation
Selecting the right materials is vital in PCB manufacturing, as it directly impacts the board’s performance and durability. WINOW collaborates with trusted suppliers to source high-quality materials, such as copper-clad laminates, solder masks, and substrate materials. These materials are then prepared and cut into appropriate sizes according to the design specifications. The copper layers are thoroughly cleaned and coated with a layer of photoresist to facilitate the subsequent etching process.
Stage 3: Inner Layer Imaging
The inner layer imaging stage involves transferring the digital design onto the copper layers of the PCB. WINOW utilizes advanced imaging technology to achieve high precision in this process. A photosensitive layer, known as the photoresist, is exposed to UV light through the digital image, effectively creating the circuit pattern on the copper. The areas exposed to light harden, while the unexposed areas remain soluble.
Stage 4: Etching
Etching is a pivotal stage in PCB manufacturing, as it removes excess copper and leaves behind the desired circuit pattern. The PCB is submerged in an etching solution, which dissolves the unprotected copper. The hardened photoresist acts as a protective layer, ensuring only the intended circuit traces are left intact. Precision and control during the etching process are crucial to maintaining the accuracy of the circuit layout.
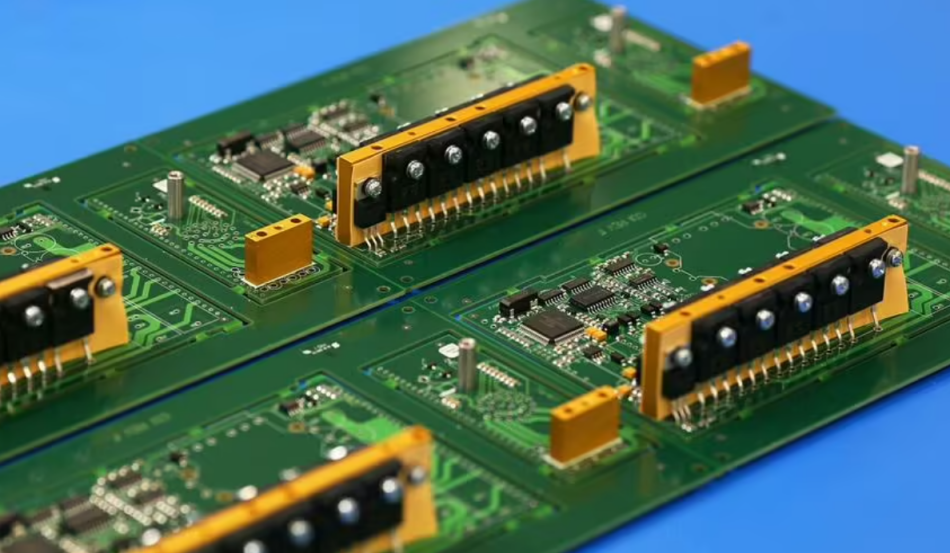
Stage 5: Outer Layer Imaging and Lamination
During this stage, the outer layer of the PCB undergoes imaging using a process similar to the inner layer imaging. Once the circuit pattern is transferred onto the outer layers, the board is laminated. High heat and pressure are applied to fuse the layers together, creating a unified and robust PCB structure. This process also ensures that all the internal connections are secure and reliable.
Stage 6: Drilling and Plating
Precision drilling is carried out to create holes for component mounting and interconnection purposes. After drilling, the holes are plated with a conductive material, typically copper, to establish electrical connections between different layers of the PCB. This ensures smooth signal flow and electrical conductivity throughout the board.
Stage 7: Solder Mask Application
A solder mask is applied to the PCB to protect the copper traces from oxidation, dust, and other contaminants. The solder mask also facilitates the soldering process during assembly and prevents unintended short circuits. WINOW uses automated processes to apply the solder mask accurately and consistently.
Stage 8: Silkscreen Printing and Surface Finish
The final stage involves silkscreen printing, where essential information such as component reference designators, logos, and part numbers are added to the PCB surface. Additionally, the PCB surface is treated with a surface finish, such as HASL (Hot Air Solder Leveling) or ENIG (Electroless Nickel Immersion Gold), to improve solderability and enhance the board’s overall performance.
How to Find the Best PCB Board Manufacturing?
1. Understanding Your PCB Requirements
Before embarking on the search for the best PCB board manufacturing manufacturer, it is essential to have a clear understanding of your project’s specific requirements. Consider factors such as the board’s size, complexity, material type, number of layers, and any special features like impedance control or high-temperature tolerance. Having a well-defined set of requirements will help you evaluate manufacturers more effectively.
2. Reputation and Experience
Reputation and experience are fundamental aspects to look for in a PCB manufacturer. Established manufacturers like WINOW often have a track record of delivering quality products and services. Check customer reviews, testimonials, and ratings to gauge their reputation in the industry. An experienced manufacturer will have better knowledge of design, production processes, and potential challenges, ensuring smoother project execution.
3. Quality Assurance and Certifications
The quality of the PCB boards is of paramount importance. Ensure that the manufacturer follows stringent quality assurance measures throughout the manufacturing process. ISO certifications, RoHS compliance, and UL approvals are indicators of a manufacturer’s commitment to quality and adherence to industry standards. WINOW, as a reputed manufacturer, is known for maintaining high-quality standards in its PCB production.
4. Technological Capabilities
In the rapidly advancing electronics industry, it is essential to choose a manufacturer with up-to-date technological capabilities. Modern PCB designs often require advanced equipment and manufacturing techniques. Check if the manufacturer employs state-of-the-art machinery, software, and processes to meet your specific design requirements. WINOW invests in cutting-edge technology to offer its customers the best-in-class PCB solutions.
5. Customization and Prototyping Services
The ability to customize PCB boards according to your project’s unique requirements is a significant advantage. Choose a manufacturer who can provide prototyping services, as it allows you to test the design before full-scale production. WINOW offers comprehensive customization options and rapid prototyping services, reducing the time to market for your products.
6. Timely Delivery and Support
Time is of the essence in electronics projects. Ensure that the PCB manufacturer has a reliable track record of timely deliveries. Consider their production capacity and turnaround time for bulk orders. Additionally, look for a manufacturer that provides excellent customer support, as it can be crucial during the design and production stages. WINOW is known for its prompt deliveries and responsive customer service.
7. Cost-effectiveness
While quality should never be compromised, cost-effectiveness is undeniably an important factor to consider. Obtain quotes from multiple manufacturers and compare their pricing structures. Remember to assess the overall value offered, considering factors such as quality, lead time, support, and additional services. WINOW strives to provide competitive pricing without compromising on product quality.
Conclusion
PCB board manufacturing is a sophisticated process that requires precision, attention to detail, and cutting-edge technology. As a prominent manufacturer in the industry, WINOW follows a meticulous approach throughout the entire manufacturing journey. From design and prototyping to surface finish, each stage plays a vital role in producing reliable and efficient PCBs that power the electronic devices we rely on daily. Understanding this process technology enables manufacturers like WINOW to deliver exceptional products, contributing to advancements in technology and enhancing user experiences across various sectors.