PCB Fabrication and Assembly: Achieving Optimal Results
The modern age of technology is powered by printed circuit boards (PCBs). To guarantee the maximum performance of these electronics, meticulous attention to detail must be given when executing the fabrication and assembly processes. In this guide, we will look at all the necessary steps and apply the expert knowledge of Winow New Energy Company, a top-tier manufacturer in this field.
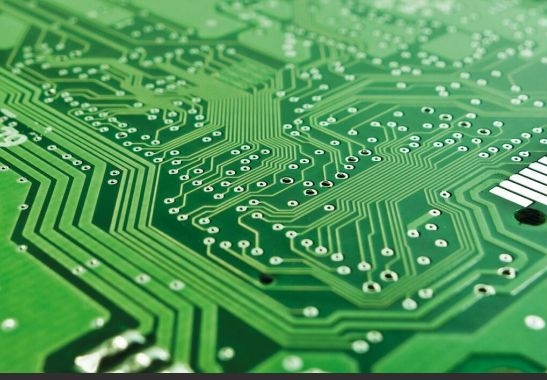
I. Choosing the Right Manufacturer
Finding a reputable manufacturer is the first step toward successful PCB fabrication and assembly. Winow New Energy Company has established itself as a trusted partner for PCB solutions. Their extensive experience, state-of-the-art facilities, and commitment to quality make them an ideal choice for all your PCB needs.
II. PCB Design and Prototyping
A. Design Considerations:
1. Component Placement: Proper component placement is crucial for efficient PCB assembly. Consider factors such as signal integrity, thermal management, and accessibility during the design phase.
2. Trace Routing: Efficient routing of traces helps ensure signal integrity and minimize interference. Avoid crossing different signal lines to prevent signal crosstalk.
3. PCB Layer Stackup: Choose an appropriate layer stack-up based on your design requirements, considering factors such as signal integrity, power distribution, and board size.
B. Prototyping:
1. Design Validation: Before moving into full-scale production, it is essential to validate the PCB design through prototyping. This step helps identify and rectify any design flaws or performance issues.
2. Rapid Prototyping: Winow New Energy Company offers rapid prototyping services to expedite the design iteration process. Their advanced equipment allows for quick turnaround times without compromising on quality.
III. PCB Fabrication
A. Material Selection:
1. Substrate Material: The choice of substrate material depends on the application requirements, such as temperature, signal speed, and reliability. Common materials include FR-4, FR-6, and flexible materials like polyimide.
2. Copper Thickness: Determining the appropriate copper thickness ensures efficient current-carrying capacity and signal transmission.
B. Manufacturing Process:
1. Panelization: PCB panelization involves arranging multiple boards on a larger panel for efficient manufacturing and assembly.
2. Etching and Plating: This process involves etching away excess copper using chemical solutions and plating the remaining copper to create conductive traces.
3. Solder Mask Application: Applying a solder mask layer protects the PCB surface and defines the areas where the solder should and should not adhere during assembly.
4. Silkscreen Printing: Silkscreen printing adds component labels, reference designators, and other markings to the PCB for easy identification and assembly.
IV. PCB Assembly
A. Surface Mount Technology (SMT):
1. Component Placement: SMT involves placing surface-mount components onto the PCB using automated pick-and-place machines. Precision and accuracy are essential for reliable soldering.
2. Reflow Soldering: Reflow soldering melts solder paste, creating a reliable electrical and mechanical connection between the components and the PCB.
B. Through-Hole Technology (THT):
1. Component Insertion: THT components have leads that pass through pre-drilled holes in the PCB. Proper alignment and secure insertion are critical for robust connections.
2. Wave Soldering: In wave soldering, the PCB with inserted components passes over a wave of molten solder, forming strong solder joints.
V. Quality Assurance and Testing
Winow New Energy Company ensures strict quality control measures throughout the fabrication and assembly processes. They employ advanced testing techniques, including automated optical inspection (AOI) and in-circuit testing (ICT), to detect any defects or faults and ensure product reliability.
Ⅵ. PCB Fabrication and Assembly: Common Mistakes to Avoid for a Flawless End Product
PCB fabrication and assembly play a crucial role in the manufacturing process of electronic devices. From simple consumer gadgets to complex industrial equipment, the quality and reliability of printed circuit boards (PCBs) are paramount. To achieve a flawless end product, it is important to be aware of common mistakes that can occur during the fabrication and assembly processes.
1. Design Stage Mistakes
Insufficient Clearance and Trace Spacing: One of the most common mistakes in PCB design is inadequate clearance and trace spacing. Insufficient spacing between traces or between a trace and a pad can lead to electrical shorts or signal interference. It is crucial to follow design guidelines and ensure the proper clearances specified by the manufacturer. Winow New Energy Company emphasizes the importance of thoroughly reviewing design rules and double-checking clearance requirements to avoid potential issues during fabrication and assembly.
Improper Component Placement: Poor component placement can result in difficulties during assembly, hindering the manufacturing process and potentially affecting the functionality of the PCB. Components placed too closely together or in inconvenient locations can impede proper soldering or cause thermal problems. It is essential to consider factors such as heat dissipation, accessibility for testing and debugging, and ease of assembly when placing components on the PCB.
2. Fabrication Stage Mistakes
Neglecting Design for Manufacturing (DFM) Guidelines: Failure to adhere to Design for Manufacturing (DFM) guidelines can lead to costly and time-consuming issues during PCB fabrication. Ignoring DFM guidelines may result in problems such as improper panelization, inadequate solder mask clearance, or incomplete drill hole registration. Winow New Energy Company stresses the importance of collaborating closely with PCB manufacturers, sharing design files early in the process, and actively seeking their input to ensure smooth fabrication.
Inaccurate Gerber File Generation: Gerber files contain the manufacturing instructions for PCB fabrication. Generating inaccurate or incomplete Gerber files can result in critical errors, such as misaligned solder masks, missing copper traces, or incorrect drill hole placements. To avoid these issues, it is crucial to carefully generate and review Gerber files before sending them for fabrication. Thoroughly inspecting the files for potential errors will minimize the chances of manufacturing defects.
3. Assembly Stage Mistakes
Insufficient Solder Paste Application: Achieving a reliable solder joint is essential for the proper functioning of the PCB. Insufficient or excessive solder paste application can lead to solder joint defects, including poor wetting, insufficient fillet formation, or tombstoning. Following the recommended solder paste guidelines, accurately depositing the right amount of paste, and ensuring proper stencil alignment during the solder paste printing process are key factors in avoiding these problems.
Inadequate Quality Control Measures: Neglecting rigorous quality control measures during PCB assembly can result in the delivery of flawed end products. Failure to perform thorough inspections, functional testing, and adherence to industry standards can lead to faulty components, improper solder joints, or electrical connectivity issues. Winow New Energy Company emphasizes the importance of implementing robust quality control protocols, including automated optical inspection (AOI) and in-circuit testing (ICT), to ensure high-quality PCB assemblies.
Conclusion:
Achieving high-quality PCB fabrication and assembly requires expertise, precision, and attention to detail. Winow New Energy Company offers comprehensive solutions, from design prototyping to final production, ensuring that your PCBs meet the highest standards of performance and reliability. By following this guide and partnering with a trusted manufacturer like Winow New Energy Company, you can confidently embark on your PCB fabrication and assembly journey.